Ferro
Para acessar o desenho artístico do elemento ferro,
clique aqui.
Mapa da chave
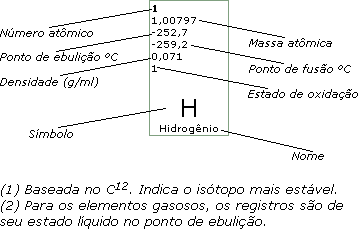
26 55,847 3.000 1.536 7,86 2,3
Fe
Ferro
|
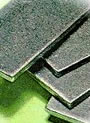 |
Amostra de ferro |
A revolução industrial, iniciada na Grã-Bretanha no fim do século
XVIII, representou a transição da sociedade agrária e têxtil para a
sociedade industrial, que se baseava no carbono, como combustível, e
no ferro, como matéria-prima fundamental para a fabricação das
máquinas. Conhecido desde os tempos pré-históricos, o metal dá nome
à idade do ferro, período histórico que sucedeu a idade do bronze.
Pertencente ao grupo dos metais de transição, o ferro é o quarto
elemento químico em abundância na crosta terrestre. É um sólido
branco-acinzantado, de densidade 7,8, que funde a cerca de 1.530º C,
passando ao estado pastoso. É o principal corpo ferromático e
altamente suscetível à corrosão pelo ar úmido, que o transforma em
ferrugem, óxido férrico hidratado, sendo por isso indispensável
protegê-lo. Em presença do oxigênio e do cloro, incendesse ao rubro,
e decompõe o vapor da água, liberando oxigênio. Na natureza,
apresenta-se principalmente combinado com o oxigênio em forma de
óxidos: hematita (Fe2O3), magnetita (Fe3O4),
limonita (Fe2O3NH2O) e siderita
(FeCO3). O minério de ferro, fundido, tem múltiplas
aplicações e grande utilidade industrial.
Propriedades físicas e químicas:
Há duas séries principais de ferro: os compostos ferrosos,
nos quais o ferro é divalente, e os compostos férricos nos
quais é trivalente. Entre os primeiros, citemos o óxido FeO negro e
o sulfato FeSO4, que
se apresenta hidratado em belos cristais verdes; esses compostos são
redutores. O óxido férrico Fe2O3, vermelho, ou
colcotar, que serve para polir vidro, o cloreto FeCl3
e o sulfato Fe2(SO4)3, que servem
para coagular o sangue, pertencem à segunda série. Citemos ainda o
óxido salino ou óxido magnético Fe3O4, que
constitui a pedra-ímã natural.
Quando puro, o ferro é um metal branco-cinzento brilhante.
Caracteriza-se pela grande ductibilidade, que permite transformá-lo
em fios e arames, e maleabilidade, que facilita a fabricação de
folhas laminares. Entre suas propriedades físicas destaca-se o
magnetismo, que o torna um ótimo material para fabricar ímãs. Quanto
às propriedades químicas, o ferro é inalterável, em temperatura
normal, quando exposto ao ar seco. Submetido ao ar úmido, o ferro
metálico sofre oxidação e se transforma lentamente em ferrugem
(óxido de ferro), o que pode ser evitado se o ferro for revestido de
metal mais resistente à corrosão, como zinco (ferro galvanizado),
estanho (folha-de-flandres) ou cromo (ferro cromado). O ferro é
atacado facilmente por ácidos.
Obtenção e aplicações:
A elaboração do ferro puro diretamente da do aço por uma refinação
particular no forno de soleira ou no forno elétrico, em presença de
escórias (ferro armco). Processos especiais de tratamento por um
redutor sólido ou gasoso, de decomposição de carbonila ou eletrólise
permitem obter, em quantidades, em quantidades reduzidas, certas
quantidades de ferro em forma de esponja ou de pó. Utilizado por sua
maleabilidade, sua pouca dureza, sua grande resistência ou seu
ferromagnetismo doce (permeabilidade, fraco campo coercitivo), o
ferro puro industrial é difícil de destingir, em suas aplicações, do
aço extradoce (ferro com 10% de carbono). Empregam-no, por exemplo,
com finalidades eletromagnéticas (ferro doce para peças de
eletroímãs, chapas de indução de motores).
Ferroligas:
As ligas do tipo ferro-carbono podem ser classificadas em quatro
grupos distintos: (1) aço doce, liga que contém menos de 0,06% de
carbono e cuja estrutura é essencialmente ferrosa; (2) aços, ligas
com conteúdo de carbono entre 0,06% e 2%, que se subdividem em aços
ao carbono, aços-ligas e aços especiais ou aços finos; (3) ferro
fundido, liga que contém mais de dois por cento de carbono, em geral
de reduzida ductibilidade e maleabilidade, utilizada na fabricação
de peças moldadas e tubos; (4) ferroligas. No aço, a dureza está na
razão direta da percentagem de carbono na liga.
As ferroligas são compostas de ferro com um ou mais elementos em
proporções adequadas para aproveitamento industrial ou para a
introdução de novos elementos na própria liga. Na siderurgia, são
matérias-primas fundamentais e sua falta impossibilitaria a produção
de vários produtos siderúrgicos. As ferroligas convencionais são:
ferromanganês, ferrossilício, ferrossilício-manganês e ferrocromo,
presentes na quase totalidade dos processos de produção de ferro e
aço comum ou especial. As ligas não convencionais, como ferroníquel,
ferromolibdênio e ferrotitânio, entre outras, servem como veículo
para adição de elementos de liga na produção de aços especiais.
Os aços-ligas são denominados segundo os metais que contêm, seu uso
ou suas propriedades notáveis. Tem-se, assim: aço-cromo, aço-níquel,
aço-molibdênio; aços para ferramentas; aços inoxidáveis; aços para
produção mecânica (rolamentos e molas) e outros.
História:
Admite-se que o ferro tenha sido descoberto quando, no período
neolítico, fragmentos desse minério, que circundavam as fogueiras
feitas para aquecer os homens nas cavernas, foram reduzidos a metal
sólido pelo calor e o contato com a madeira carbonizada.
Encontraram-se contas de ferro nas tumbas de al-Gezirat, Egito,
datadas de 4000 a.C. As escavações feitas na área da antiga cidade
de Ur, na Caldéia, revelaram a existência de um artesanato
incipiente de ferro no terceiro milênio antes da era cristã. Os
portões da Babilônia de Nabucodonosor, no século VI a.C., foram
reforçados com ferro. Entre os chineses, o uso do ferro remonta pelo
menos a 2250 a.C. Na Bíblia, o Gênesis menciona Tubalcaim, artífice
de todo instrumento cortante, de bronze e de ferro.
A exploração de jazidas de ferro começou a ser feita com
regularidade em torno de 1500 a.C., provavelmente no Oriente Médio,
de onde o metal teria sido importado por assírios e egípcios. A
primeira referência escrita ao metal consta de uma mensagem dirigida
por um imperador hitita ao faraó Ramsés II, no século XIII a.C., do
primeiro milênio da era cristã em diante, o ferro difundiu-se por
toda a bacia do Mediterrâneo.
Acredita-se que o ferro, a princípio, tenha sido obtido por um
processo que não chegava a extraí-lo do minério, nem a liquefazê-lo,
mas tornava-o maleável. Dessa forma também se fundem outros minérios
associados ao de ferro, que se combinam e transformam-se em escória.
Em estado incandescente, a escória pode ser separada da massa, o que
dá, como produto final, um bolo de ferro. Com o metal desses bolos
foram fabricados os primitivos instrumentos de trabalho, como
machados, martelos e pontas-de-lança.
A principal fonte de abastecimento de ferro da Roma antiga foi a
península. O metal servia como matéria-prima do gladius
hispanus, espada curta de dois gumes usada pelos legionários.
Após a queda do Império Romano, desenvolveu-se na Espanha a
fabricação de objetos de ferro. Tornaram-se famosas as lâminas de
aço de Toledo, que rivalizavam com as de Damasco. As forjas catalãs,
de cuja evolução se originaram os grandes fornos, estenderam-se à
França e à Alemanha e serviram para a fabricação de ferramentas e
armas.
Na forja catalã, que dominou a produção de ferro até o século XV, o
ar frio é insuflado na fornalha por meio de foles manuais. O carvão
de madeira é posto na lareira e, quando se acha em brasa, é coberto
por uma camada de minério, à qual se seguem camadas justapostas de
carvão e minério, ficando a última ao lado do fole. Insuflado o ar,
o carvão se queima e se processa então, a redução do minério a
metal.
Após diversas experiências e inventos, chegou-se ao alto-forno em
meados do século XV. O ferro obtido em alto-forno tem o nome de
ferro-gusa, ferro fundido ou simplesmente gusa. As temperaturas mais
elevadas permitiram que o ferro absorvesse mais carbono que carvão e
se transformasse em gusa, o qual sai do forno em estado líquido
incandescente. Modernamente, o minério de ferro, além da fabricação
do gusa, também é aproveitado para a manufatura de pigmentos,
cimento, gás purificado e gás hidrogênico, bem como na fundição de
várias ligas metálicas. A maior parte da produção mundial destina-se
à indústria siderúrgica.
Produção brasileira:
Instalou-se em São Paulo o primeiro forno de ferro da América, no
fim do século XVI. Os de Jamestown, na Virgínia, Estados Unidos, são
posteriores a 1607. O mineral havia sido descoberto no Brasil, no
início do século XVI, pelos jesuítas, que logo passaram a fabricar,
com o metal obtido na forma primária da redução do minério, anzóis,
facas e outros tipos de ferramenta.
Uma importante descoberta foi a da jazida de Ibirapuera, à esquerda
do rio Pinheiros, onde morava Afonso Sardinha, que descobriu ferro
em Biraçoiaba, próximo a Sorocaba - SP. Afirma-se que em 1590,
Sardinha começou a explorar a mina. Em 1597 comunicou o fato a
Francisco de Sousa, governador-geral do Brasil, e doou a jazida ao
rei de Portugal. Sousa passou a zelar pela extração do minério,
razão pela qual mereceu o título de marquês das Minas.
Disseminou-se em Minas Gerais e São Paulo o processo de fabricação
de ferro em forjas e cadinhos. O metal era utilizado para ferrar
cascos de animais de tração e em aros de carros de bois. Em 1785, a
rainha D. Maria I proibiu o funcionamento de fábricas no Brasil,
fato que deu especial significado político à fabricação do ferro,
transformada num dos ideais de emancipação dos inconfidentes. Com a
transferência da corte portuguesa de Lisboa para o Rio de Janeiro,
D. João VI incumbiu, em 1808, o intendente Câmara (Manuel da Câmara
Ferreira Bethencourt e Sá) de instalar uma fábrica de ferro no morro
do Pilar. A primeira corrida de ferro-gusa desse alto-forno foi em
1814. Antes disso, em 1812, o barão de Eschwege obtinha ferro
líquido em sua fábrica em Congonhas - MG.
O rei incumbiu também Francisco de Varnhagen de instalar uma fábrica
de ferro em São João de Ipanema, posterior Sorocaba SP. Essa
iniciativa destacava-se das anteriores, de tipo artesanal, e marcou
o início da indústria siderúrgica no Brasil, em 1818. Pouco tempo
depois, o engenheiro de minas francês Jean-Antoine Félix de
Monlevade, dito João de Monlevade, instalou uma fundição de ferro
perto de Caeté - MG.
Foi a partir de 1921 que realmente se iniciou o desenvolvimento da
produção brasileira de ferro-gusa, com a instalação de diversos
altos-fornos. Já em 1936 fabricavam-se no país cerca de oitenta mil
toneladas. Com a instalação, em 1941, da Companhia Siderúrgica
Nacional, em Volta Redonda RJ, a produção de ferro iniciou uma nova
época de desenvolvimento com incentivo estatal. No fim do século XX,
o Brasil figurava entre os três países possuidores das maiores
reservas conhecidas de minério de ferro em todo o mundo. Passou de
terceiro a segundo lugar após a descoberta de riquíssimas reservas
no norte de Minas Gerais e na serra de Carajás, no Pará.
Produção mundial:
O ferro é de longe o primeiro mineral metálico extraído, com uma
produção mundial, em crescimento desacelerado, da ordem de 500
milhões de toneladas (mineral contido). A Rússia fornece 1/4
desse total, antepondo-se claramente a Austrália, cuja produção (80
milhões de toneladas) cresceu, porém, rapidamente e já ultrapassou
dos E.U.A. (40 milhões de toneladas). Bem atrás, segue-se um grupo
de produtores médios, cada qual extraindo de 20 a 40 milhões de
toneladas de metal contido (Canadá, China, Sibéria e índia). Base da
siderurgia, o ferro é objeto de importante comércio internacional,
voltado sobretudo para a Europa do Mercado Comum, onde a França é o
único produtor notável (11 milhões de toneladas). No Brasil, a
produção de ferro (minério) alcançou 139.696.000 toneladas em 1980,
o que coloca em terceiro lugar mundial de minério.
Propriedades físicas e químicas do ferro:
|
Número atômico: |
26 |
Peso atômico: |
55,847 |
Ponto de fusão: |
1.535º C |
Ponto de ebulição: |
3.000º C |
Densidade: |
7,86 |
Estados de oxidação: |
+2, +3, +4, +6 |
Configuração eletrônica: |
(Ar) 3d6 4s2 |